Energiatehokkuus ja energiansäästö (Järjestelmät, laitteet ja ohjelmistot, Kulutuksen ohjaus ja kysyntäjousto)
Energiatuotanto ja -jakelu (Kompressorit, Painelaitteet ja putkistot)
Käyttö ja kunnossapito (Tarkastus, testaus)
Paineilmaa säästämällä parannusta tuotantoprosesseihin
Monissa teollisuuden prosesseissa tarvitaan paljon paineilmaa, jonka valmistukseen voi kulua melko suuri osuus teollisuuslaitoksen koko energiankäytöstä. Jo pienilläkin korjaustoimilla voidaan säästää paineilmaa ja energiaa – tuotannon määrästä tai laadusta tinkimättä.
Paineilma on kokoon puristettua eli paineistettua ilmaa, jota käytetään moniin tarkoituksiin muun muassa teollisuudessa ja terveydenhuollossa. Kokoon puristettaessa ilman paine, tiheys ja lämpötila kasvavat.
Paineilman tuotanto on keskeinen osa teollisuuden prosesseja. Niinpä sen tehokkuus on olennainen kysymys, kun pyritään hillitsemään energiankulutusta ja tuotantolaitosten operatiivisia kustannuksia.
Ongelmia ei aina tiedosteta
Paineilmakompressorit kuluttavat teollisuuden sähköenergiasta joskus jopa 18 prosenttia.
Tyypillisesti paineilman käyttöä tehostavien toimenpiteiden kannattavuus on tapauskohtaista. Siihen vaikuttavat muun muassa laitoksen koko sekä laitteistojen ikä ja huoltotarve.
Osa säästöistä voidaan saada aikaan jo pelkästään puuttumalla käyttö- ja huoltotottumuksiin. Laitoksilla voidaan myös korjata vuotokohtia ja investoida vaikkapa lämmöntalteenottoon tai uuteen ohjausjärjestelmään.
Usein teollisuuslaitoksilla suhtaudutaan paineilmaan itsestään selvänä hyödykkeenä, jonka tuottamiseen kulutetun energian määrää ei välttämättä ymmärretä eikä sen kulutusta säädellä. Paineilman tuotanto vaatii erityisosaamista, joten se on teollisuudessa usein ulkoistettu.
Kun käytetään ulkoistettua palvelua, voidaan keskittyä laitoksen keskeiseen toimintaan. Toisaalta ulkoistetun palvelun käyttö saattaa johtaa siihen, että laitoksen oma tietämys ja kiinnostus paineilmajärjestelmän kuntoa ja tehokkuutta kohtaan jää kenties vähemmälle huomiolle.
Paineilman tuotanto on keskeinen osa teollisuuden prosesseja.
Verkkovuodot vaikuttavat
Yhden paineilmakuution saaminen 7 barin paineeseen vie sähköä ehkä noin 0,1 kilowattituntia (kWh). Kun otetaan huomioon vuodot ja muut paineilmajärjestelmän tekniset ongelmakohdat sekä huoltokulut, kokonaiskustannukset lisääntyvät.
Kaikki paineilmajärjestelmät vuotavat jonkin verran. Vuotojen määrä vaihtelee laitteistotyypin, laitteiden iän ja kunnossapidon mukaan. Alle viiden prosentin vuotoa voisi vielä pitää hyväksyttävänä, mutta konepajateollisuudessa 20 – 30 prosentin vuodot voivat olla melko tavallisia.
Usein järjestelmien mitoituksessa varaudutaan 10 prosentin vuotoon. Yleensä vuodot eivät ole niinkään putkissa olevia reikiä, vaan erilaisia tiiviste- ja venttiilivuotoja.
Aluemyyntipäällikkö Sami Lanttola Oy Atlas Copco Kompressorit Ab:stä huomauttaa, että optimaalisen ja energiatehokkaan paineilman tuotanto on monitahoinen kysymys.
On tärkeää ymmärtää eri kompressorityyppien toimintaperiaatteet ja niiden soveltuvuus eri käyttöolosuhteisiin, hän sanoo.
Kun pyritään paineilman säästöön, on otettava huomioon mahdolliset vuodot paineilmaverkostossa ja optimoitava painetaso. Edelleen on huolehdittava säännöllisestä huollosta, ja mahdollisesti valittava oikeanlainen keskusohjaus. Paineilman ja energian säästämiseksi voidaan siis tehdä paljon.
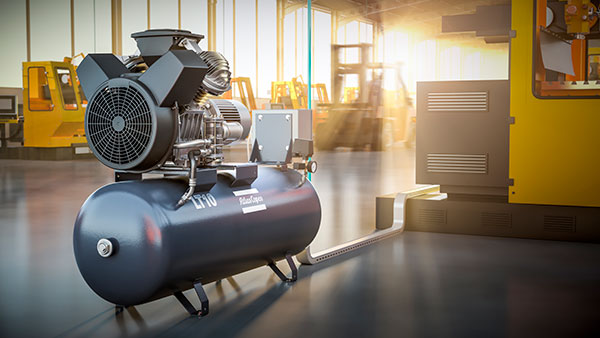
Lisää suorituskykyä
Lanttolan mukaan yksi tehokkaimpia energiasäästömahdollisuuksia esimerkiksi konepajoilla olisi siirtyminen muuttuvatuottoisiin taajuusmuuttajaohjattuihin kompressoreihin.
Tällaisten kompressoreiden kierrosnopeus säädellään tarkasti tarpeen mukaan, mikä vähentää energiankulutusta ja sopeuttaa kompressorin käyttöolosuhteisiin.
Kierrosnopeus voi vaihdella kulutuksen mukaan, jolloin kompressori sopeutuu dynaamisesti käyttöolosuhteisiin. Esimerkiksi Atlas Copcon muuttuvatuottoisissa kompressoreissa ei esiinny kevennyskäyntiä. Lisäksi ne on suunniteltu suoravedolla – ilman mekaanisia välityksiä – mikä eliminoi voimansiirron häviöt ja maksimoi suorituskyvyn, Lanttola kuvailee tekniikkaa.
Paineilmaa voidaan tuottaa kahdella menetelmällä: käyttämällä joko kiinteätuottoisia tai muuttuvatuottoisia kompressoreita.
Kiinteätuottoisten kompressoreiden mitoituksessa on olennaista tarkkuus, jotta laitteen tuottama paineilma vastaa mahdollisimman tarkasti tarvittavaa määrää.
Jos mitoitus tehdään vain likimääräisen arvion perusteella, se voi johtaa koneen ylimitoitukseen ja siten aiheuttaa niin sanottua kevennyskäyntiä. Silloin sähkömoottori pyörii tyhjäkäynnillä suojatakseen moottoria liiallisilta käynnistysmääriltä.
Tämä ominaisuus kuluttaa noin 30 prosenttia sähkömoottorin nimellistehosta ilman paineilman tuotantoa, mikä on merkittävä energianhukka. Muuttuvatuottoisissa kompressoreissa, jotka ovat taajuusmuuttajaohjattuja, ei ole tätä ongelmaa, Lanttola tähdentää.
Paineilman tuotannon optimointiin kuuluu myös paineilmavuotojen kartoittaminen.
Tuotannon optimointia
Atlas Copcossa on arvioitu, että optimoimalla paineilmajärjestelmää yritykset voisivat kohtuullisen helposti säästää yli 30 prosenttia energiaa. Parhaissa tapauksissa säästöt voivat olla jopa 50 prosentin luokkaa.
Esimerkiksi Atlas Copcolle patentoidun tekniikan ansiosta energiansäästöpotentiaali verrattuna saman teholuokan kiinteätuottoisiin kompressoreihin keskimäärin 50 %.
Paineilman tuotannon optimointiin kuuluu myös paineilmavuotojen kartoittaminen, joka voi paljastaa merkittäviä säästöpotentiaaleja. Vuotojen tunnistaminen ja korjaaminen vähentää tarpeetonta energiankulutusta ja parantaa järjestelmän kokonaistehokkuutta, Lanttola muistuttaa.
Painetason optimointi on toinen tärkeä askel. Sillä varmistetaan, että paineilmaa tuotetaan vain tarvittava määrä, jolloin vältetään ylipaineen aiheuttamaa energiahukkaa.
Oikeanlaisen ohjaustavan valinta – kuten keskusohjaukset useampaa kompressoria käytettäessä – mahdollistaa järjestelmän tasapainoisen ja tehokkaan toiminnan.
Keskusohjausjärjestelmät voivat optimoida useiden kompressorien käyttöä, mikä vähentää tarpeetonta kuormitusta ja parantaa energiatehokkuutta.
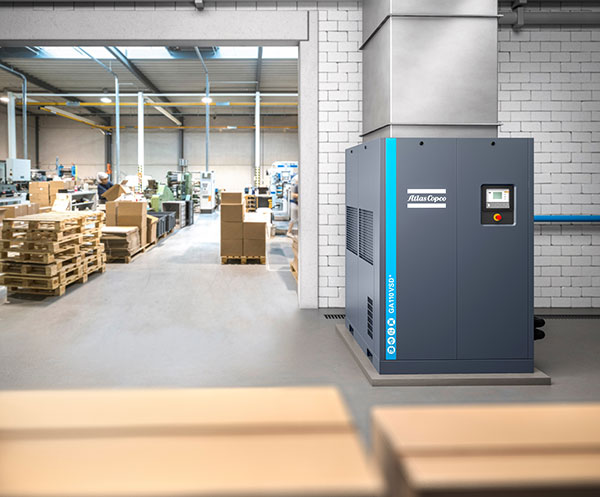
Lämpöä talteen
Edelleen puristuslämmön talteenotto voi edesauttaa energiatehokkuutta.
Paineilman tekemisessä käytetään sähköenergiaa, joka muuttuu lämmöksi. Lämmöstä jopa 90 – 95 prosenttia voidaan ottaa talteen ja hyödyntää sitten esimerkiksi tuotantotilojen lämmittämisessä.
Esimerkiksi joissakin Atlas Copcon öljyvoidelluissa ruuvikompressoreissa on sisäänrakennettu ER-levylämmönvaihdin, jonka avulla lämmöntalteenotto on tehokasta, Lanttola mainitsee.
Innovatiivisen teknologian ansiosta kompressorista voidaan ottaa lämpöenergiaa talteen tyypillisesti noin 75 – 80 prosenttia sähkömoottorin nimellistehon verran. Tämä lämpöenergia on mahdollista siirtää veteen, minkä jälkeen sitä voidaan hyödyntää monipuolisesti vaikkapa lämmitysjärjestelmissä, käyttöveden lämmittämisessä tai prosessilämpönä erilaisissa teollisissa sovelluksissa.
Tämä ei ainoastaan lisää energiatehokkuutta ja vähennä käyttökustannuksia, vaan myös tukee kestävän kehityksen tavoitteita. Oikein suunniteltuina teollisuuden laitteet voivat olla sekä suorituskykyisiä että ympäristöystävällisiä. Silloin fossiilisten polttoaineiden tarve vähenee ja hiilijalanjäljet pienenevät.
Energiatehokkuutta olisi mahdollista parantaa oikea-aikaisella ja ammattitaitoisella huollolla.
Tarkkuutta suunnitteluun
Jos prosesseihin tehdään tehokkuutta parantavia muutoksia, ne tulee suunnitella huolella.
Parhaimpaan lopputulokseen yleensä päästään, kun pystytään yhdessä yhteistyökumppanin sekä mahdollisesti suunnittelijan kanssa keskustelemaan käyttäjän tarpeista, toiveista sekä käyttötarkoituksesta, Lanttola arvioi.
On siis hyvä ottaa mukaan paineilma-asiantuntija jo suunnitteluvaiheeseen. Yhteisvoimin löydetään varmasti energiatehokkain ja luotettavin ratkaisu juuri omaan tarpeeseen. Suunnittelussa otetaan huomioon käyttötarve, ilmanvaihto, energiatehokkuus, optimaalinen sijoittelu sekä erilaiset lisämahdollisuudet, joilla voidaan hyödyntää paineilmatuotantoa kokonaisuutena.
Lisää säästömahdollisuuksia syntyy tutkimalla kulutusprofiilia. Esimerkiksi Atlas Copco suorittaa Airchitec-mittauksia, joista nähdään paineilman kulutusprofiili ja nykyisen järjestelmän energiakulutus viikon pituiselta mittausjaksolta.
Näistä tiedoista laaditaan simulaatio, jossa vertaillaan nykyistä järjestelmää optimaalisempiin ratkaisuihin. Näin saadaan selville todelliset säästömahdollisuudet euroina, energiamäärinä ja jopa CO2-päästöinä.
Energiatehokkuutta olisi Lanttolan mukaan mahdollista parantaa myös oikea-aikaisella ja ammattitaitoisella huollolla.
Kompressorien pitkäikäisyyden ja luotettavuuden kannalta on todella tärkeää käyttää alkuperäisosia ja asianmukaisia voiteluaineita. Säännöllisen huollon avulla varmistetaan, että kompressorit toimivat optimaalisella teholla ja minimoidaan odottamattomien vikojen riskiä.
Teksti: Ari Mononen
Kuvat: © Atlas Copco Group
Kirjallisuutta:
Hagner, Börje: Energiakatselmoijan käsikirja. Motiva Oy, Helsinki.
Piilonen, Maija: Paineilmajärjestelmän energiatehokkuuden kehittäminen. Jyväskylä (2020).